Efficient horizontal gas-liquid separator is China patent product designed and manufactured by Ningbo Xingbang Biochem. Device Company, also strongly recommended by Chinese Biological Fermentation Industry Institute. It is precisely manufactured by stainless steel, and widely applied in fermentation air treatment system with remarkable economic benefits. Disposal capacity of a single separator can reach 10Nm3/min ~3000Nm3/min, and hundreds sets are in service in industries.
Basic Principle
Air inlet and outlet lies in a line, with many separation units inside; Apply centrifugal separation and collision condensation principle; moisture droplets >5μm will accumulate in diameter after collision than be removed by separation units, the water collection will drain through bottom outlet. This equipment overcome the problem of how separation efficiency and high pressure loss which exist among traditional high air-volume handling.
Features
Wide volume range of air-handling
Process volume of a single separator is 100m3/h~180000m3/h, which satisfies modern mass production demand.
High separation efficiency
While handling high air volume, the efficiency reaches to 98%-99.99%, removing the dust and impurities completely. 20% higher efficiency than normal separator (normal cyclone and plate collision water separator)
Low Resistance
Pressure loss between (0.5kPa ~2kPa), energy-saving.
Good adaptability to air flow fluctuation
stable separation efficiency when dealing with air volume fluctuation; overcome short-comings of efficiency fluctuation of traditional separators.
Compact structures
Under same air handling capacity, compact structure with small footprint, easy for installation, cost saving.
Easy for automation
continuous to drain, easy to operate.
Long service life
precision manufactured with stainless steel. No easy-wearing part inside, no packing or other media requiring regular replacement, no clog, almost free of maintenance. Traditional wire mesh mist eliminator, when handling high air volume, the efficiency drops due to enlarged diameter, and the resistance of packing wire elevates with a high risk of jam, and wire replacement requires a production stop. However horizontal separator avoid all the above-mentioned problems.
Comparison with Other Kinds of Separators
Traditional gas-liquid separation process in air treatment usually use cyclone or wire mesh mist eliminator or folding plate separator, which exist many defects.
(1)Traditional cyclone separator is only suitable for use of a constant air rate condition, for the use of gas-liquid separation, the aerosol water can hardly be separated, so the result is undesirable. The separation efficiency under the working condition of strong air rate fluctuation is low, generally between 60% ~ 80%; and there exists prominent contradiction between resistance loss and separation efficiency, the smaller the droplet diameter, the higher the airflow speed, and the greater the airflow resistance losses are. As for separation under 100 microns, the resistance loss and even reached more than 20 kPa.
(2)Wire mesh demister, for processing large fermentation air volume air, requires large equipment diameter, leading to reduced separation efficiency, increased resistance and risk of clog, therefore it’s not suitable for heavy load gas-liquid separation in fermentation air treatment, and replacement of its internal parts requires production interruption.
(3)Folding plate water separator adopts the mechanism of droplet collision, but it is difficult to remove aerosol in the air with low separation efficiency only around 75%, and its dust removal effect is poorer, and the end hook of the folded plate is easily filled with impurities, undermining separation efficiency and even causing system failure.
To remove aerosol, moisture or dust in the air stream with low resistance, application of efficient horizontal gas-liquid separator is most ideal.
Therefore in terms of gas-liquid, gas-dust separation in air pretreatment system, now use efficient horizontal gas-liquid separator to replace the conventional cyclone, wire mesh demister and fold plate water separator. Energy saving effect is remarkable, and the air quality is further improved.
Applications
- Gas-liquid separation to obtain sterile air in the fermentation industry, to remove oil, moisture, steel rust and other impurities from air, to guarantee the effect the downstream air filtration media , which also extends its life. Especially suitable for high volume air pretreatment system, separate the impurities completely with small resistance, stable and energy –saving.
- Applied in the industrial fermentation exhaust air treatment system (pharmaceutical, amino acid, organic acid, enzyme and fermentation pesticide, reduce the post processing burden of (sterilization and deodorization) ;improve the fermentation environment, and reduce the waste emission.
- To replace traditional separator for gas-liquid separation. For example, the separation efficiency of cyclone is generally 60%~80%, which being washed out gradually; mesh wire mist eliminator, as for high volume air handling, due to its large equipment diameter and low separation efficiency, hard maintenance (easy to clog) affecting normal production, is not recommended; plate separator works via droplet collision, so not effective for moisture in the air, the liquid separation is as low as 75%, and its configuration is easy to get clogged with an even lower mist separation efficiency, so it doesn’t fit for high gas-liquid separation. In a conclusion, efficient horizontal separator wins out to replace traditional equipment
- Recycling of dust, fog, liquid droplet in the environmental engineering.
Structure Schematic
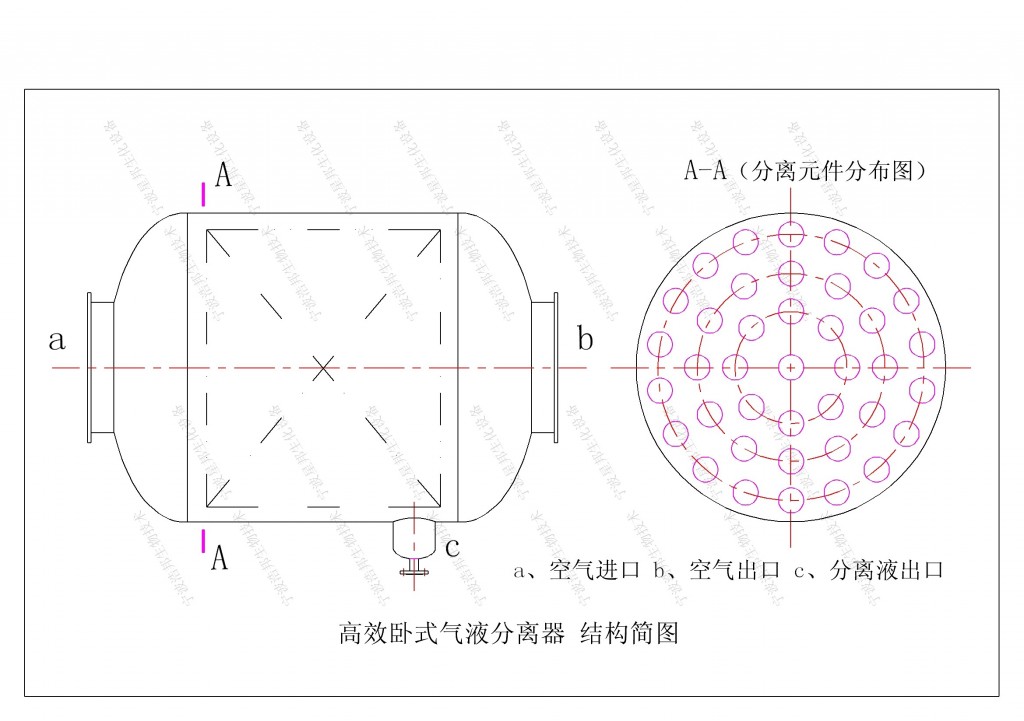