General methods to improve DO level in fermentation are modification of mixer configurations, increase of stir speed and installation of jet-tube air sparger, etc. The former two either requires a big investment or increases operational cost; The latter demands a high pressure head to achieve high jet flow speed, increasing power consumption of air compressors. At the same time, high speed flow causes shear damage of certain cells, extends batch cycle, affects target yield; and it has a complex structure with excessive connectors, thus is prone to contamination with limited applications. Vortex Gas-liquid Mixer is a new type energy-saving air sparger, and it has many merits including good performance of air dispersion, deep gas-liquid blending and good production adaptations, etc.
Technical background
Structure & Mechanism
Vortex G-L mixer has inner and outer shell. Air enters the inner shell, transformed to a high speed vortex flow vie guide vane, simultaneously, generated negative pressure drags broth into mixing aisle between shells, then air is dispersed completely by dynamic emulsification effect in the spiral flow way before jetting out .
The basic principle of vortex G-L mixer is energy conversion between static pressure and kinetic pressure of compressed air, air injection drives surrounding broth, and transforms it to a high-speed rotating biphase flow. The process of vortex mixing raises bubble residence time, increases air & liquid interface areas, and improves sterile air utilization rate.
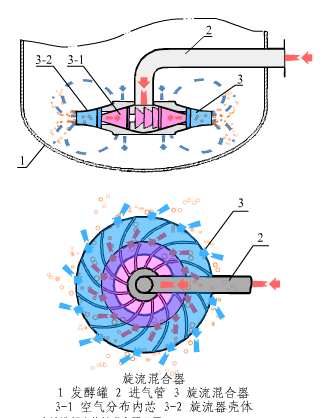
Features
1 Easy installation. Vortex gas-liquid mixer directly replace existing annular air sparger.
2 Complete gas-liquid blending at the bottom of the fermentor. Dispersed air bubbles have small diameters; DO level increases by 5% ~ 20%; better air utilization.
3 Mild mechanical interactions between cells during mixing. Target yield increases steadily.
4 Concise structure comparing to jet-tube sparger, easy to clean, free of contamination.
5 Low resistance, low demand for driving pressure head, no extra increase of compressor load or power consumption.
6 Vortex gas-liquid mixer serves not only as an air sparger, but also a bottom stirrer. In coordination with mixing system, or draft tube modification, traditional stirring can be simplified or even cancelled. It can also be used in new-type ALR.
Applications
Applied in 260m3 glutamic acid fermentors, to improve the glutamic acid conversion rate by more than 0.5%.
Used in 45m3 DHA fementors, cancelled original mixing system, reduced shaft current by 100%.
Applied in 150m3 threonine fermentors, to increase DO level by more than 10%.
Used in 150m3 erythromycin fermentors, to improve DO level by about 8%; target yield improved steadily.
Used in 110m3, 70m3 antibiotics fermentors, to reduce electricity consumption by about 8%; target yield improved steadily.
Used in 150m3 amino acid fermentors, to reduce electricity consumption by about 8%; target yield improved remarkably.
Applied in 200m3 vitamin fermentors, to reduce electricity consumption by 5%~30% and antifoam use by 1/3, with target yield improved by 2%.
Applied in 150m3 penicillin fermentors, to reduce electricity consumption by 7%~20%; target yield improved steadily.
Applied in 60m3、200m3 Steroid hormone fermentors, to reduce electricity consumption by 15%; target yield improved by more than 3%.
Applied in 140m3、325m3 vitamin C air lifter fermentors,improve DO level and target yield,and stablize liquid level.。