Aerobic fermentation needs constant sterile air supply. The heat compressed air cannot directly into the fermentation tank, and mixed bacteria and cell in the air stream must be removed. Based on the requirement of aseptic membrane filters, the compressed air must be pretreated. Usually, it be cooled below the pressure dew point, and separated from oil, water and other impurities, then it will be heated to reduce the relative humidity. In a relative cool and dry condition the air goes into the membrane filter, so that the filter can perform its function to the maximum.
System function and the defect of traditional system
System function
Defect of traditional system
Traditional fermentation air pretreatment system generally adopts two-stage cooling, two-stage dewatering and steam heating with excessive auxiliaries and a complex configuration. Due to low equipment efficiency, it requires large cooling and heating amplitude, leading to high energy consumption, high pressure loss and high power consumption; In addition, as fermentation aeration rate changes, separation efficiency of traditional separator fluctuates, leading to low dewatering effect and low air quality. In that case, processed air is difficult to meet the operational requirements of aseptic air, affecting the service life of downstream aseptic filters and production stability.
System operation parameters
System of sterile air pretreatment (SAS) consists of advanced new finned-tube cooler, high efficient horizontal gas-liquid separator and air circulatory heater. With several state key patents, it solves above-mentioned problems, provides good air quality, improves production stability, saves water, electricity, steam, and reduces system capital cost and operational cost dramatically.
Enery-saving system | Trational system | |
---|---|---|
Outlet pressure of air compresssor (MPa,G) | 0.15~0.25 | 0.25~0.4 |
Air temperature after cooling (℃) | 20~35 | 15~20 |
Air temperature after heating (℃) | 40~60 | 50~70 |
Heat source | Hot compressed air | Steam |
System pressure loss (MPa) | 0.005~0.01 | 0.01~0.05 |
Unit power (kW/ (m3/min)) | 2.5~3.5 | 3.5~5.0 |
SAS Processing Workflow
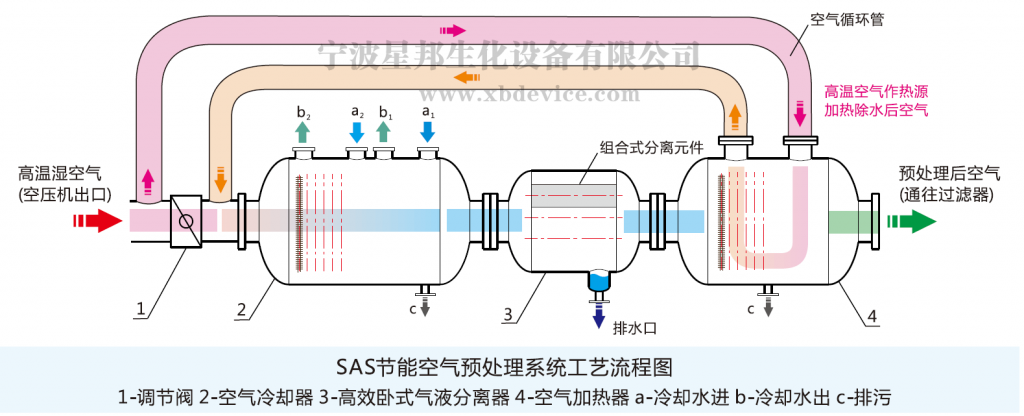
SAS Features
1 High efficiency
High heat transfer efficiency: The new-type heat exchanger adopts strenghened heat transfer unit, suitable for the physical properties of moist air, easy to descale and clean.
High separation efficency: High efficient horizontal gas liquid separation adopts design of parallel separation units, no clog, no maintenance, dewatering rate reaches 98%~99.88%, suitable for application in energy-saving air pretreatment systems.
2 Energy-saving
- Save water:,less use or no use of chilled water or cold salt water, thus reduce the operation load of chiller; the heat exchange of hot and cold air stream can reduce cooler load and save circulating cooling water of from cooling tower; multi-tube side with big temperature difference of inlet and outlet, can reduce the cooling water flow rate. Therefore the total water-saving can reach 30%~75%. And at the same time, the system supporting water pump, fan power consumption is greatly reduced.
- Save steam: cooled air must be heated to decrease relative humidity. Use hot compressed air itself as heat source instead of steam, can also meet temperature and humidity requirement. What’s more, here use advanced high efficient horizontal gas-liquid separator, to get rid of condensate, avoid extra steam consumption in traditional heating system. So the total steam saving is 80%~100%.
- Save electricity: The resistance loss of the whole system is extremely low, only 3kPa~8kPa, only 10%~50% of traditional system. Therefore, the air compressor outlet pressure can be reduced with lower shaft power input, thus the power consumption dropped significantly, and electricity saved by 5%~16%.
In accord with actual application case concluded: compared with traditional system or other pear energy-saving system. SAS has a minimum operation cost.
3 Improve air quality, stabilize production
Due to systematic high efficiency and good coordination, especially the good gas-liquid separation performance of horizontal gas-liquid separator (remove condensate and large amount of harmful microbe at the same time), This system reduce the harmful microbe density in the air stream dramatically, and improve outlet air quality, and leading to better performance, longer service life, fewer number of filter sterilization replacement and extend normal production time and improve the production stability.
On the other hand, the air heater uses the hot air circulation heating, which is the most reliable way of all heat source. As long as the air compressor is normal, stable system operation is guaranteed, which is not affected by factors other than air pretreatment itself. For example, if steam or hot water is used as heat source, the supply interruption will threaten the system. And in the air heater there is no pressure difference between shell side and tube side, eliminated the risk of tube cracking and leakage, which will seriously impair normal production.
4 Horizontally deployed in a line, convenient for installations
5 Internal heat balance
As for air circulation exchange, the heat is internally balanced, thus the system can adaptively absorb the impact of air rate fluctuation or environment temperature or humidity change. Even without automatic control module, robust fermentation production can be realized, and the normal operation and maintenance is convenient.
Cooler Features
- Finned-tube to strengthen heat transfer, high efficiency, durable.
- Low flow velocity in the shell, low pressure loss.
- Multi-stage cooling arrangement, able to use multiple coolant (circulating water, chilled water, etc.)
- Tubes vertically deployed, drain outlet at bottom of every stage to release impurities.
Horizontal Separator Features
- Patent technology design, stainless steel precisely manufactured.
- Parallel separation units, separation efficiency 98%~99.99%, good adaptation to aeration volume rate fluctuations.
- Remove aerosol by collision and centrifugation completely, reduce impurities dramatically and improve air quality.
- Separation efficiency 20% higher than cyclone (only 60%~80), 15%~25% higher than folded plate separator. Compared to screen separator, more reliable, far less pressure loss, and no clog.
- No wearing parts, free of maintenance, extended life.
Heater Features
- Use compressed hot air as heat source, no steam needed, energy-saving, free of disruptions from steam system malfunction.
- Specially designed: make up defects of traditional gas-gas heater, with low resistance and high heat transfer efficiency.
- No pressure difference between tube an shell in gas-gas heat transfer, eliminate tube crack and leakage; great reliability.
- Durable finned tube with strengthened heat transfer.