Efficient helix-strike separator (Fig.1) is a fermentation gas-liquid separator applied in broth & foam recycling system of fermentor off-gas。 The off-gas enters the equipment in a radial direction. The separator has a central tube with air deflectors and a stabilizer at the bottom. Though the process of collision, centrifugation and stabilization, foam and aerosol in the off-gas can be separated and recollected. Its performance is evaluated at a leading level at home and abroad. Our company has independent intellectual property rights over this product. Helix-strike separator has been upgraded to the 2nd generation, and is highly recommended by China Fermentation Society for its energy-saving and environmental protective performance.
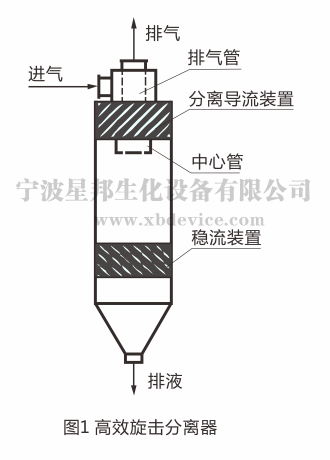
Performance Features
1 High separation efficiency
Gas-liquid separation efficiency 98%-99.99%; 20% higher than the traditional cyclone.
2 Good aeration fluctuation adaptation
When aeration volume rate fluctuates, its separation efficiency can be maintained at a high level, which is unparalleled in contrast to other separators.
3 Low pressure loss
Far less than screen separators and folded plate separators.
4 No dead coner, easy cleaning and sterilization,anti-scale
5 Anti-corrosion, extended life
Precisely manufactured with stainless steel. No moving part, very less wear, basically free of maintenance.
6 Compact structure
Slender profile, small footprint, easy to install, convenient for automatic control.
7 Great cost performance
With a high performance, the price is only 1/5 ~ 1/4 of imported similar products. Besides, we successfully developed a series of super large Helix-strike separators with processing capacities of 20000 m3/h ~ 50000 m3/h.
Applications
1 Oil-water separation of sterile air preparation in fermentation industry
2 Applied in broth recycling in fermenter off gas
Broth recycling, avoid broth escaping
During certain aerobic fermentaion production, broth escapes from the reactor in the form of foam, droplets in off-gas, leading to broth loss and environment contamination. When H-S separators installed, escaped broth can be separated from the droplets and foam, then collected back to reactor to form a circulation, finally processed clean air goes out from the top (Fig.2).
In that case, fermentor capacity increases without increase of antifoam consumption. Since separation efficiency of a H-S separator is among 98%~99.99% with a good adaptation ability of volume rate fluctuations, aerosol can also be recycled, so it is highly suitable for off-gas treatment.Reduce antifoam consumption
Although antifoam is still necessary for production, H-S separator is able to break foam. When there is no foam escaping in off-gas, there is no need to add antifoam. So the anti-foam consumption can be lowered by 1/5~1/2.
Increase reactor capacity
As for certain products with excessive foam and severe broth escaping, it has to lower the capacity to keep the broth at a low level. When installed with H-S separator, reactor capacity can be raised by 5%~15%, therefore, the production volume increases significantly, without increasing resource consumption or labor input.
Stabilize production
Since no broth escaping, cell density in the off-gas precipitates by 4 orders of magnitude in comparison with no H-S separator installed case. Therefore, the production environment is improved, miscellaneous microbe in the air is under control, filter load is decreased, and there forms a virtuous circle to produce sustainable economic benefits.
Lower downstream processing load and cost
H-S separator can be used as primary treatment device of fermentation off-gas disposal. it will reduce workload of downstream deodorization and sterilization process, and lower operational cost.
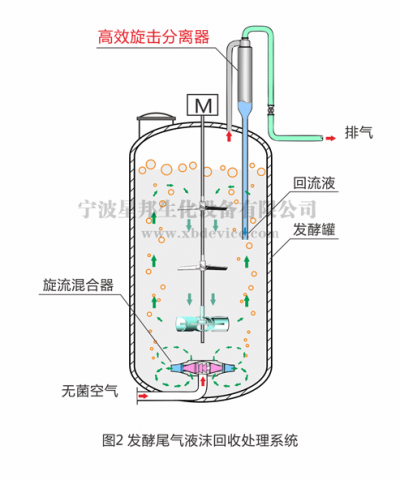
3 Applied in gas-liquid separation of chemical reaction off-gas
In Biochemical or organic synthesis reactions, organic off-gas usually goes through cooling, condensation, then enter H-S separators to realize the recycle of organic liquid .
4 Air purification from water and dust in automation instrument and spray paint industries
5 Air purification of large factory space
6 Gas-liquid, gas-dust separation in the environmental protection industry , reduce PM2.5 emissions
Installation schematic of high efficient helix-strike separator
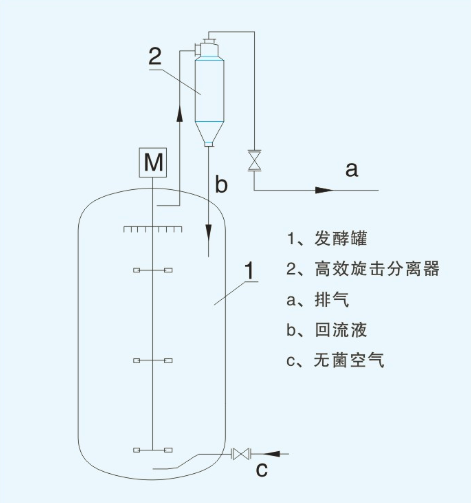